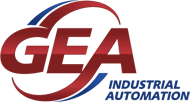
Guaranteeing packaging results every time, even when product characteristics vary and product types change often, is one of the greatest challenges facing a machine builder. This was the primary consideration for Alpenland Maschinenbau (ALPMA) when designing its new MultiSAN film wrapping machine. The machine packages round and rectangular soft cheeses, as well as cheeses in karospar, cylindrical and half-moon formats.
“There are cheese makers today that make only a few types of cheese, but nevertheless change over their production every two or three hours because they produce every order by the truckload,” said Helmut Eitermoser, the designer of the MultiSAN. The reasons for smaller and smaller batches are typically the same as in other industries: customer-specific product requirements, shorter product life cycles and increasing product variety.
Until now, cheese makers used packaging systems in which a mechanical master shaft with cam drives mounted on it drove the synchronous motion of the individual mechanisms.
ALPMA’s film wrapping machine called the MultiSAN can process a range of products with no changeover with use of LinMot linear motors.
“These cam machines were, and continue to be, the right solution for packaging just one type of product. They are precise, cost-effective and durable,” said Eitermoser. Two similar format shapes—such as round and half-moon—and different sizes with the same shape can also be processed on these machines with a reasonable effort. This does, however, require a compromise; the packages for each product version are less than optimal. “When several different products are to be packed in a folded or wrapped package on the same machine with rapid changeovers, the cam machine reaches its limit. Reconfiguration or even machine replacement is required before a product changeover.
For the MultiSAN, the ALPMA design team used direct-drive technology in combination with a virtual master shaft and electronic cams, which have completely replaced their mechanical counterparts.
The envelope folds under the cheese, typical for wrapped packaging, are now produced by means of four horizontally mounted LinMot linear motors that each drive one shutter blade through a linkage. Once the cheese has been wrapped in the packing film by the machine, and has been fixed in place on a round plate by a gripper, the shutters press the protruding film together on the bottom of the product in rapid succession, thus producing the desired fold pattern. Another linear motor axis moves the cheese off of the round plate onto a belt that transports the cheese to the next station.
For this specific application, the design team suspected early on that only linear motors would have the power density that they needed. “Demo units have shown that rotary servomotors are not well suited for this task because they take up too much space,” said Eitermoser. He chose model PS01-23x160H-HP-R motors for the MultiSan. The motors have a diameter of 23 mm (stator)—not including the plug connection on the end—but nevertheless are able to produce a peak force of 130 N when coupled with the E1130-DP-HC controller.
The matching sliders are available as standard products in many variants, for strokes from 20 to 780 mm. The version selected for the MultiSAN has a stroke of 120 mm.
The space-saving form factor of the linear motor also allows the new design to take up the same floor space as the comparable version with a mechanical master shaft. The cycle time also match: both run at up to 80 cycles.
By using direct-drive technology, the MultiSAN has been decoupled mechanically so that sensitive components can be folded back out of the foam cleaning area.
The commonalities end there, however. To create a much more modular construction, the ALPMA design team combined the mechanical unit with the shutter drives into one module that is used in several places on the machine. It is designed to function as a heat sink for the linear motors as well. These features all helped lead to a product with consistent and repeatable results every time.
“We have also made use of the sensitive and direct reaction performance of the linear motors to give the operator an instrument for reacting to variations in product consistency,” said Eitermoser. “The responsible parties on-site can thus set their own parameters for various consistencies, so that the machine operator can adapt the machine settings to changes in product characteristics just by pushing a button.”